TYPES OF WELDING JOINTS
TYPES OF WELDING JOINTS
What is Welding Joint?
Welding is a process that needs patience, detail, and creativity. To perform it successfully, welders should have an understandable knowledge of the various methods and practices used in the industry, also including types of welding joints.
A welding joint is referred to an arrangement or configuration of two metal plates that will be fit together. The purposes of welding are infinite, and different processes require different types of welds and joints.
According to the American Welding Society (AWS), there are 5 basic additions that are commonly known and applied. These welding joint types are each stands for the needs and forces of different applications. So, let’s discuss them one by one.
Types of Welding Joints
Following are the 5 main types of welding joints:
- Butt joint welding
- Lap joint welding
- Edge joint welding
- Tee joint welding
- Corner joint welding
1. Butt Joint Welding
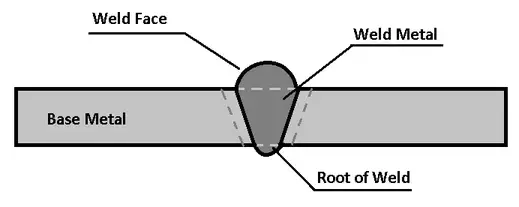
These types of welding joints form when the two metal pieces are placed end to end together in the same plane surface, it is known as butt joint welding. In welding, this is the most common type of joint.
Usually, butt joint welding is used for the fabrication of structures, welding pipes, valves, fittings, and others. Well, it is simple to prepare, and there are many variations that can be applied to obtain the desired result.
These variations include such as angles, the width of the gap, groove shape, root, and weld size. Following are some typical examples of butt weld joints that are included in welding.
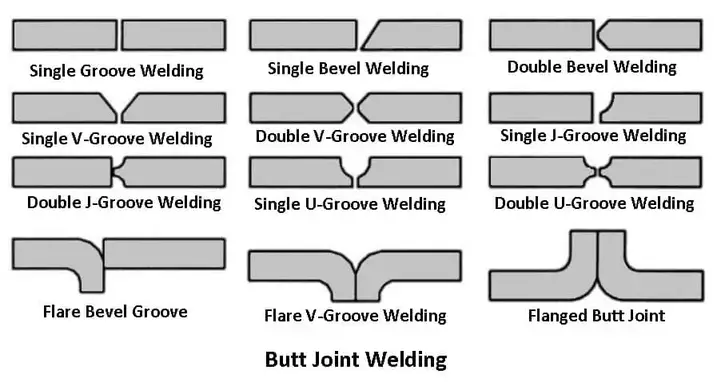
- Square welding
- Single bevel welding
- Double bevel welding
- V-groove welding
- Double V-groove welding
- U-groove welding
- Double U-groove welding
- J-welding welding
- Double J-groove welding
2. Lap Joint Welding

It is basically a modification of butt welding, in which the two metal plates are placed in an overlapping position that is on top of each other, it is known as lap joint welding.
The lap joint welding is applied for welding two metal plates that are different in their thickness. In this, welding can be done on both sides of the plates for greater strength.
It is widely used in the combined electron beam, laser beam, and resistance spot welding. Lap joints are rarely used on thick materials, and most of the time also used for sheet metal. While doing lap joint welding, you will face some drawbacks.
Those are lamellar tearing or corrosion due to the overlapping metals. But, you can easily handle them by applying the correct technique and modifying the variables as required. Following are the typical examples of lap joint welding,

- Fillet welding
- Spot welding
- Plug welding
- Slot welding
- Bevel groove welding
- Flare bevel groove welding
- J-groove welding
3. Edge Joint Welding

This is quite similar to the lap joint. In this, both the metal plate surfaces are placed together, that they are adjacent and generally parallel in position at the point of welding. It is known as edge joint welding.
It is formed by bending both plates at an angle. In edge joint welding, the same edge of two plates is welded. However, this is not a very strong joint because the weld does not fully penetrate the joint thickness.
Because when the two metals have a contact area, corrosion will occur. Therefore, create defects such as porosity, lava inclusion, and lack of fusion, like any other type of joint.
Hence, it is often used for joining the edges of sheet metal or mufflers, and in other applications like low stress and pressure. Following are the examples that applicable in edge joints.

- V-groove welding
- U-groove welding
- J-groove welding
- Bevel groove welding
- Square groove welding
- Corner flange welding
- Edge flange welding
4. Tee Joint Welding
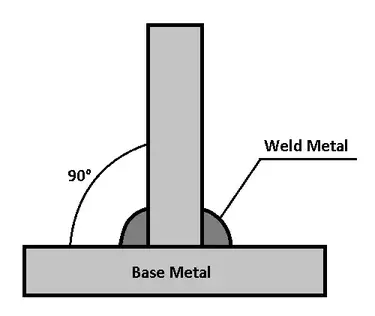
It is formed, when the two metal plates are intersected to an angle of 90° with one plate is lie on the center of the other plate like a “T” shape. It is known as tee joint welding.
These types of welding joints are considered the use of fillet welds mounted on both sides. It is formed when a pipe is welded over a base metal. Commonly, tee joints are prepared with grooves, until the base metal is thick.
But, again you will a drawback in the tee joint, which is lamellar tearing. It is caused by the limitation experienced by the joint. If you want to handle this, you will need to place a stopper to prevent joint damages. Following are examples of tee joint welding.

- Plug welding
- Slot welding
- Bevel groove welding
- Flare bevel groove welding
- Fillet welding
- J-groove welding
- Melt through welding
5. Corner Joint Welding

It is almost similar to the tee joint welding, the only difference is that in the position of the metal plates. As compared to the tee joint, plates are placed in the middle, whereas in the corner joint, both the plates meet in either an open or closed way to form a shape like “L”.
These joints are some of the common types in the industries of sheet metals, such as in the manufacture of boxes, frames, and other applications. The drawbacks like lamellar tearing, incomplete penetration, porosity, slag inclusion, etc. will occur in the corner joint.
A small variation can be applied to reduce the appearance of these defects. Variations like grooving welded metal and using an open corner joint rather than a closed corner joint. Following are the typical examples of corner joints.

- Fillet welding
- Spot welding
- Edge welding
- J-groove welding
- U-groove welding
- V-groove welding
- Flare V-groove welding
- Square or butt groove welding
- Corner flange welding
- Bevel groove welding
Comments
Post a Comment